Cornerstone Automation’s cost-effective solution improved efficiency and flexibility for the passivation process of a leading medical device manufacturer.
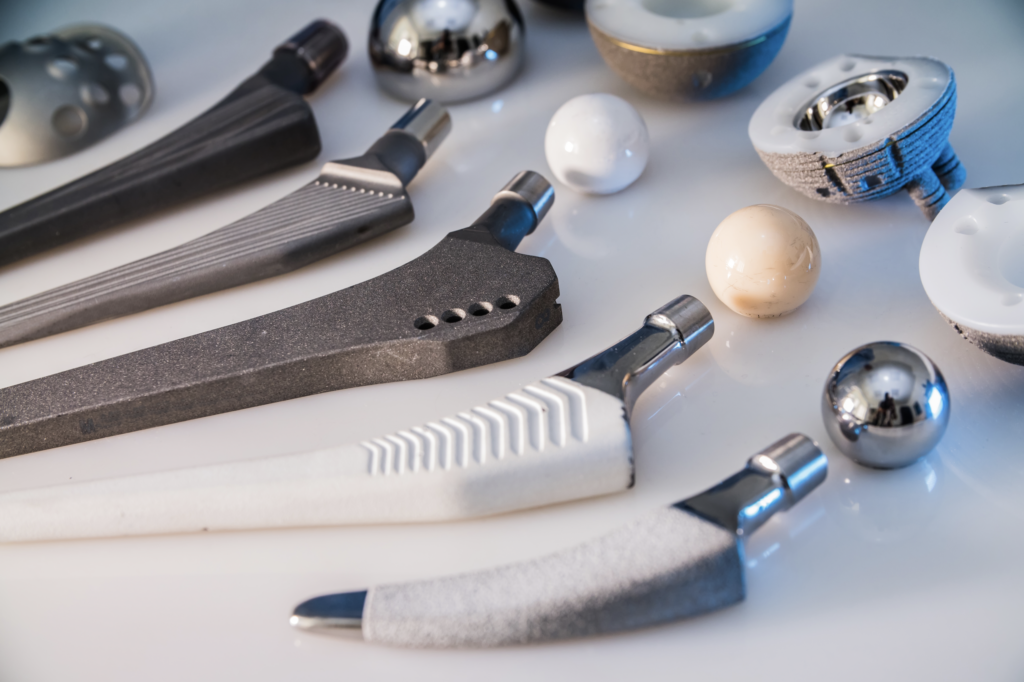
Challenge
A leading medical device manufacturer had a passivation line that facilitates an essential process on their stainless steel medical parts. Passivation is creating a protective coating on stainless steel parts through a chemical reaction between oxygen and chromium by removing any iron particles on the surface of the parts. On a passivation line, stainless steel parts are cleaned, etched, and finally dipped into a passivation bath (often combined with other finishing methods.) The medical device manufacturer had bought the line from a company called Blackstone-NEY Ultrasonics. The manufacturer had run it, but there were customer requirements that it couldn’t perform. Thus, they began outsourcing the passivation of materials to a third party and the machine only was used for the light cleaning process.
The medical device manufacturer was looking for local support to address the issues on the line. After investigation, Cornerstone engineers found and repaired several broken sensors, and once they got the line running, they configured the machine to use the passivation vats that were not used previously.
The parts need to be put in a basket, then lifted and dipped into different process tanks for specified amounts of time as the product traveled down the line.
“We have a sonic passivation clean line that all of our manufactured products go through,” explained the maintenance manager at the leading medical device manufacturer. “It involves CitriSurf sonic tanks, wash baths, and heaters. It’s a pretty sophisticated piece of equipment that is all automated. Cornerstone Automation backed up the Allen Bradley software, which was really important. That line is vital to our process; if that piece is not running, we can’t ship anything.”
Solution
The leading medical device manufacturer learned about Cornerstone Automation when they had issues with a bag sealer used for packaging in one of their buildings. Upon the recommendation of mechanist, Ed Randolph, an acquaintance of Alan and Nathan, the maintenance manager reached out to Cornerstone Automation to fix the equipment, which started the relationship between the two companies.
Cornerstone Automation provided a solution to customize the line for the medical device manufacturer. Cornerstone programmed both the HMI and PLC to use whichever wash station was available and run both stations simultaneously to make the entire process faster. They also allowed for an option to bypass the passivation station because certain products can’t be run through it. Parts that bypass the passivation stations are washed separately with a different chemical process.
A recipe guide was programmed by Cornerstone Automation so that operators could pull parameters quickly using the HMI menu. The recipes were existing, but the Cornerstone engineers added recipe parameters to modify the way the sequence would operate, in turn, giving operators the ability to skip one of the passivation tanks or use both in parallel. The leading medical device manufacturer had started making new products that could not make contact with the passivation liquid, but still needed to be washed. All work was completed on-site in about 3 days’ time.
“Cornerstone has come back several times now,” said the maintenance manager. “One time Alan came in and cleaned all the control boxes in the cabinet, which were full of graphite dust. Another time they had to make an adjustment to the controls. There was a pH sensor issuing situation that was malfunctioning due to the way the control was reading. The company that built the equipment was unable to help, so I relied on Cornerstone to fix it, and their engineer was here for less than half an hour, he fixed it and he was out the door. Another example of how reliable Cornerstone Automation is and how they take care of business.”
Equipment Used:
- Blackstone NEY ultrasonic cleaner
- Allen Bradley SLC500 PLC
- Allen Bradley PanelView Plus 1000 HMI
- PowerFlex 40 VFDs
- Encoders
Results
- Customized solution allowed for more flexibility and efficiency in the production line
- Programming of HMI and PLC allowed for the use of two wash stations simultaneously, increasing throughput and speed of the process
- New products that could not make contact with the passivation liquid but still needed to be washed were accommodated by the customized solution.
- Option to bypass the wash station was provided, allowing for certain products to be washed separately with a different process
- Recipe guide programmed by Cornerstone Automation allowed for quick parameter pulling using the HMI menu
- Recipe parameters were added to modify the sequence, giving operators the ability to skip one of the passivation tanks or use both in parallel
- Client could provide a faster response to customer demand
Conclusion
The leading medical device manufacturer had a passivation line that could not perform to their customer’s requirements. They had been outsourcing the passivation of materials to a third party while their own machine sat idle for years. Cornerstone engineers replaced several broken sensors, and customized the medical device manufacturer’s line, programming a recipe guide that could modify the sequence to allow for the use of both passivation tanks in parallel or the option to bypass them. The work was completed on site in three days.
“I can’t say anything bad about Cornerstone Automation. They’ve always been there for us. They have gone over, above, and beyond,” said the maintenance manager. “I work with numerous people and multiple companies due to the abundance of equipment we have here. I’m on the phone constantly to troubleshoot things. I am very thankful for Cornerstone Automation. They are customer-oriented, straightforward, and they get the job done. I know whenever I have a problem that it’s going to be taken care of.”