Do you have an SLC 5/05? If so it’s time to take action! Adapting to technological advancements and embracing the latest innovations is essential for maintaining competitiveness and efficiency. The discontinuation of the SLC line presents a valuable opportunity to evaluate your existing systems, explore modern alternatives, and embark on a migration journey that aligns with your manufacturing objectives.
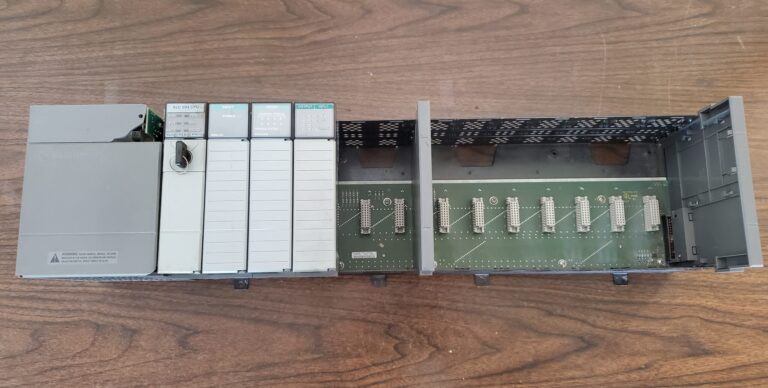
Allen Bradley’s SLC 5/05 PLC, commonly known as “Slick,” has reached a significant milestone. As the last PLC CPU produced by Allen Bradley from its line of SLC PLCs, it’s time to prepare for a strategic transition, as Allen Bradley has designated these long-standing PLCs as End of Life. End of Life means that Allen Bradley has announced a discontinued date and will gradually reduce and de-prioritize production of these parts. It’s important to note that outages may occur even prior to the official discontinued date. Now is the time to take action by strategically executing migrations and making last-time buys.
For over three decades, the SLC line of PLCs has been a staple in the automation industry. Since the introduction of the first modular SLC 500 in 1991, these PLCs have provided a more compact and streamlined alternative to the bulky PLC-5 series. With subsequent revisions released over the years, including the addition of an ethernet port on the latest SLC 5/05, these PLCs have continuously evolved to meet the industry’s demands. In the past, migrating away from earlier SLC CPU revisions typically involved a simple replacement with a 5/05 module, a process that could be completed within minutes. Now, the entire SLC line is scheduled to be discontinued (or has been discontinued) including the chassis, I/O cards, and all the processor revisions which means a more involved migration is now required.
In this era of rapid technological advancement, it is vital to stay ahead of the curve. In this article, we dive into the details of the SLC 5/05 PLC discontinuation and talk about the best practices, potential challenges, and available migration pathways. Prepare yourself and your manufacturing plant for the future by embracing the exciting opportunities that lie ahead.
Together, we can navigate the End of Life for Allen Bradley’s SLC 5/05 PLCs and unlock a new era of productivity and efficiency in medical device manufacturing.
What can you do?
Imagine a scenario where spare parts for your critical PLC systems become increasingly difficult to procure and prohibitively expensive. As a medical device manufacturing plant, you cannot afford to let costly downtime disrupt your production. The countdown to the discontinued date of Allen Bradley’s SLC5/05 PLCs has begun, and it’s time to look into a proactive solution that promises uninterrupted operations and sets you up for long-term success.
While you may be able to acquire a new PLC CPU up until the discontinued date (March 2024), the mounting costs are a cause for concern. With the current list price for the remaining SLC 5/05 processor alone coming in at over $15,000 dollars, the financial burden can quickly get out of scope. Once the discontinued date arrives, obtaining these parts will become even more difficult as new inventory ceases production. This potential downtime due to component failure can have long-term consequences on your manufacturing process and bottom line.
Luckily, there is an alternative that empowers you to take control of your future. It’s time to proactively perform a migration to one of Allen Bradley’s newer and actively supported PLC product lines. The CompactLogix 5380 often serves as an excellent migration choice, delivering enhanced performance and modern features. However, depending on your system requirements, another line might better fit your application. Rest assured, we are here to assist you in determining the most advantageous and long-lasting migration path for your equipment.
The SLC 5/05 Migration Process
Migrating to a new PLC doesn’t have to be a daunting and time-consuming process. With specialized kits and streamlined options available, your migration can be quick and seamless, minimizing interruptions to your production line. Our team is dedicated to providing the expertise and support you need to ensure a smooth transition, allowing you to focus on what matters most – manufacturing life-saving medical devices efficiently and effectively.
While some OEMs will offer migration services on their equipment, there are situations where that is not an option. Perhaps you have a custom piece of equipment, the OEM is unresponsive, or utilizing the OEM is prohibitively expensive because they no longer have the tools or personnel to support older equipment, or maybe the OEM simply no longer exists. In those cases, short of buying a new machine, a custom controls migration can be a cost-effective solution to increasing the lifespan of your equipment.
Each migration is different and depending on how complex your existing setup is, the migrations can range from a single PLC, and rewiring a handful of IO points, to a highly distributed system that can be migrated to transmit over ethernet. Cornerstone Automation can work with you to understand your facility’s needs and help you decide on the best path forward. Typically, the expense and complexity of migrations are impacted by the amount of existing documentation and/or electrical schematics for a piece of equipment.
In most cases, a migration entails:
- Assessing the scope of an existing system by using the program itself, a site visit, and any electrical schematics.
- Engineering the most cost-effective, reliable, and long-lived solution to a replacement product. This might include quick, snap-in replacement products if there are small downtime requirements.
- Implementation of the proposal by program conversion, electrical schematic updates, feature additions, and code documentation.
- Site installation and commissioning.
Benefits
First and foremost, newer electronic equipment provides improved reliability, significantly reducing the risk of unexpected failures. Beyond that, these modern PLCs offer higher availability of replacements and spare parts at more affordable prices. By embracing a strategic migration plan, you not only secure a more robust foundation for your plant but also enjoy peace of mind knowing that your critical systems are supported by readily accessible components.
The advantages of migration extend beyond reliability. Newer platforms offer unparalleled flexibility, simplifying control wiring through the utilization of advanced ethernet-based control networks. This seamless integration with managed IT infrastructure offers a world of possibilities, including opportunities for remote support & access over VPN tunnels. With email support and Industrial Internet of Things (IIoT) capabilities, these new controllers provide visibility into alternative avenues for improved productivity and operational intelligence.
What’s more, the speed of these newer PLCs can amplify the performance of your machines, driving productivity to new heights. With support for more complex instructions and expanded storage capacity, they enable superior handling of recipes and data manipulation. Additionally, these advanced options eliminate the reliance on batteries and EPROMs to maintain program integrity when the PLC power is shut off, further streamlining operations and reducing maintenance requirements.
We Can Help!
Our expert team can help you select the best migration path forward, tailor-made to suit your unique needs and objectives. Whether you have questions, or concerns, or require comprehensive support, we’re dedicated to ensuring a smooth and successful transition for your medical device manufacturing plant. Contact Cornerstone Automation today to take the first step in embracing the advantages of proactive control system migration, and protect your plant from unexpected, and costly downtime.