This case study highlights the transformative collaboration between Gold Crust Baking Company and Cornerstone Automation, showcasing the evolution of their operational technology network. From the inception of a flexible bakery system to the integration of advanced automation via the OT network, Gold Crust’s forward-thinking approach positions them as technological innovators in the dynamic baked goods industry.
Gold Crust Baking Company’s Networking Challenge
Gold Crust Baking Company, a leading player in the baking industry, approached Cornerstone Automation back in 2014 with a networking challenge within their 100,000-square-foot state-of-the-art production plant. At the time, the company was grappling with the integration of a complex mass cooling system that required flexible interconnecting and selection of many sources to numerous destination machines for product routing, interlocking, and troubleshooting purposes. This particular cooling system is not just a simple thermostat; actually, there are one hundred individual nodes all working together to keep everything at the right temperature. In addition to that, multiple PLCs that previously operated independently of one another were combined into a single supervisory system. Although Gold Crust’s IT department set up the physical network, the Cornerstone Automation team took charge of programming it.
Network Evolution and Expansion of the Bakery System
Over the years, the network expanded organically to encompass approximately 50 more systems and machines across three different lines. The unique aspect of Gold Crust’s setup lies in the flexibility of its bakery system, allowing seamless product transfer from any oven to any packaging area. “The plant has a cooling system that can take the product from any oven and deliver it to any packaging area,” explained Alan Ferrin, President of Cornerstone Automation. “It’s the most flexible bakery system I’ve ever seen. Despite the evolving and dynamic nature of the project, our team was instrumental in the initial setup, overseeing various iterations, expansions, and modifications.” In one significant development, the Cornerstone engineers rewrote the code entirely, enhancing automation and simplifying future modifications. The Programmable Logic Controller (PLC) was integrated and programmed to automatically determine available paths based on the current conveyors in use, further optimizing the system’s efficiency.
Optimizing Operations and Network Cleanup
As Gold Crust Baking Company continued to grow, Cornerstone Automation’s involvement extended beyond the initial physical network installation. In recent collaborations, the engineers’ focus shifted to addressing inefficiencies and disorganization within the network racks, a critical aspect of ensuring the system’s resilience.
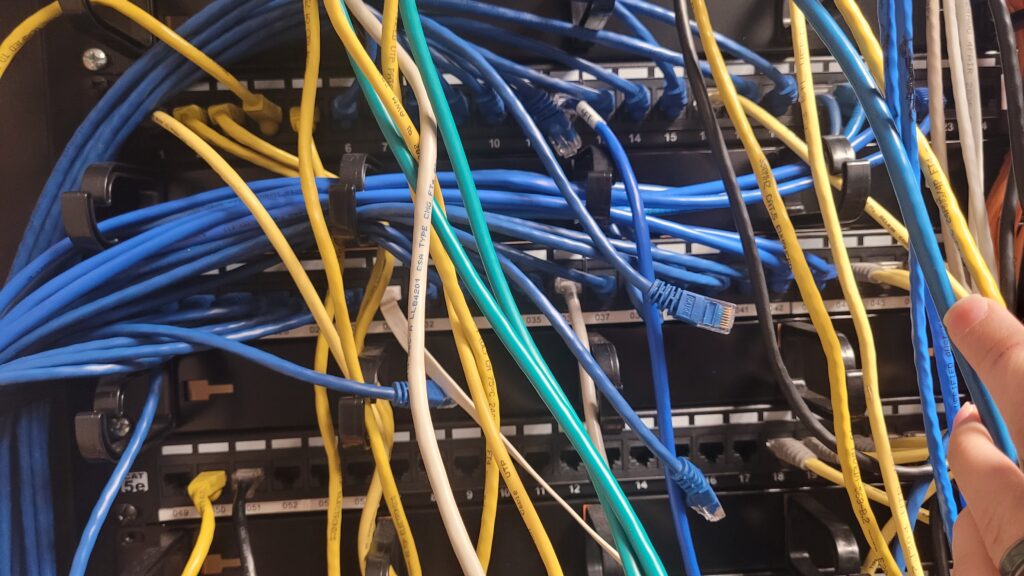
Organizing the racks had a dual purpose: facilitating easier troubleshooting and enabling remote maintenance. Engineers, armed with labeled and organized racks, could efficiently guide on-site staff to identify specific components, streamlining the troubleshooting process. The cleanup process addressed a tangle of cables on the floor, including damaged fiber optic. Further organization was required due to the inevitable evolution of hurried expansion over time that had occurred over time. This sentiment is applicable here: Why is there never enough time to do it right the first time, but always enough time to do it over? The team embarked on an extensive process of repairing and replacing the compromised cables, ensuring the network’s integrity and reliability.
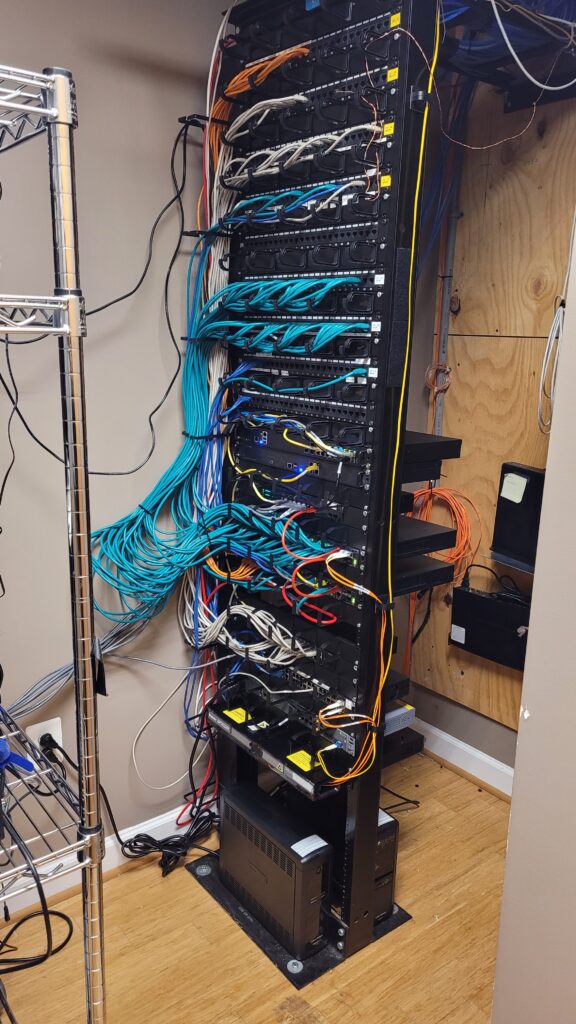
Overcoming Connectivity Challenges with Fiber Optics
In the face of connectivity challenges, the engineering team navigated and resolved issues related to lengthy connections, reaching up to 30+ feet. Beyond this threshold, the use of fiber optics became imperative due to noise constraints in conduits filled with high-voltage equipment. To address these challenges in low-voltage communications, significant amounts of multi-mode fiber optics were strategically deployed, ensuring a reliable and noise-resistant communication infrastructure.
The rack, housing both OT and IT equipment, underwent a transformation. Cornerstone engineers terminated all cables not on the patch panels, replaced fiber optics, and upgraded select Ethernet switches. Cable management was also implemented, which is a crucial element in maintaining a tidy and efficient setup.
Network Speed Upgrade and Segregation
A significant enhancement involved the upgrade of the IT network from one gigabit per second to 10 gigabits per second. This enhancement greatly improved data transfer capabilities, facilitating a more efficient and responsive network infrastructure. The team also implemented the strategic segregation of the information technology and operational technology networks using separate Ethernet switches and firewalls.
The segregation not only bolstered security but also streamlined communication and access protocols, ultimately simplifying troubleshooting for plant personnel. With distinct reporting for information technology and operational technology network issues, Gold Crust’s staff could swiftly and accurately address any issues that arose, ensuring minimal disruption to their operations.
Operational Technology Network’s Role in Automation and Flexibility
The operational technology network played a pivotal role in implementing new technology and automation previously unavailable to Gold Crust’s systems. This transformation resulted in projects running concurrently, focusing on automation, increased productivity, and improved quality. The network’s capability to facilitate line interlocking and recipe sharing between equipment showcased its pivotal role in modernizing operations, providing a level of flexibility previously challenging for manufacturers, particularly in the dynamic field of baking.
In the realm of bakeries, the ability to share recipes and perform product tracking was once groundbreaking, but today, it stands as a testament to Gold Crust’s forward-thinking approach to leveraging technology to enhance production efficiency and flexibility.
Transformative Integration for Operational Excellence
Gold Crust Baking Company’s collaboration with Cornerstone Automation marked a transformative journey in enhancing its operational efficiency and flexibility. The network’s evolution, spanning over the years, saw significant milestones, from the inception of a flexible bakery system to the implementation of advanced automation through the operational technology network. Gold Crust’s forward-thinking approach and comprehensive solutions not only modernized their operations but also positioned them at the forefront of technological innovation in the dynamic landscape of baking. This case study illustrates a successful integration that marries technological prowess with operational flexibility, setting the stage for sustained growth and adaptability in the competitive baking industry.